Energy-saving TSRM
submersible motors
TECHNICAL PROPERTIES
Power range | 1.5 – 18.5 kW |
---|---|
Mains frequency | 50 or 60 Hz |
Coolant/medium temperature | max. 60 °C |
Shaft seal | Silicon carbide mechanical seal |
Immersion depth | max. 20 m |
TECHNICAL SPECIFICATIONS
TSRM size 132
Type | Nominal power ratings | Current rating | cos φ | Rotation speed | Weight | |
---|---|---|---|---|---|---|
kW (P2) | kW (P1) | A | rpm | kg | ||
TSRM 16-132 | 1.5 | 1.8 | 3.55 | 0.74 | 965 | 92 |
TSRM 26-132 | 2.2 | 2.5 | 5.1 | 0.74 | 965 | 94 |
TSRM 34-132 | 3.0 | 3.5 | 5.9 | 0.83 | 1,450 | 98 |
TSRM 44-132 | 4.0 | 4.6 | 7.8 | 0.83 | 1,450 | 98 |
TSRM 54-132 | 5.5 | 6.1 | 11 | 0.83 | 1,450 | 105 |
TSRM 74-132 | 7.5 | 8.4 | 15 | 0.83 | 1,450 | 108 |
TSRM 114-132 * | 11.0 | 12.4 | 21 | 0.85 | 1,450 | 127 |
Motor 400 V, IE2 (IE3 can be selected), rated frequency 50 Hz, index of protection IP 68 | * Energy efficiency class IE1 |
Energy-saving motors have higher inrush currents due to their design!
TSRM size 160
Type | Nominal power ratings | Current rating | cos φ | Rotation speed | Weight | |
---|---|---|---|---|---|---|
kW (P2) | kW (P1) | A | rpm | kg | ||
TSRM 74-160 | 7.5 | 8.2 | 13.8 | 0.87 | 1,450 | 122 |
TSRM 114-160 | 11.0 | 12.2 | 21.0 | 0.84 | 1,450 | 141 |
TSRM 154-160 | 15.0 | 16.5 | 28.0 | 0.85 | 1,450 | 161 |
TSRM 184-160 | 18.5 | 20.2 | 34.7 | 0.84 | 1,450 | 173 |
Motor 400 V, IE2 (IE3 can be selected), rated frequency 50 Hz, index of protection IP 68
Energy-saving motors have higher inrush currents due to their design!
DIMENSIONAL DRAWING/DIMENSIONS [MM]
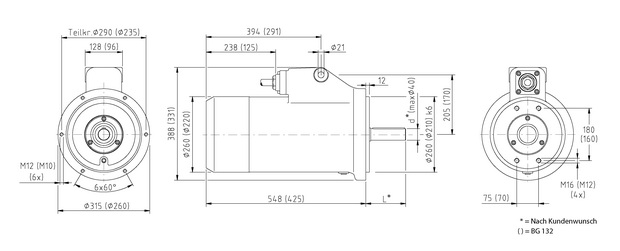
MATERIALS
Housing | GG25 |
---|---|
Flanges | GG25 |
Connecting elements | Stainless steel 1.4301 (V2A) |
Motor shaft | Heat-treated steel (stainless steel available if requested by the customer, at extra cost) |
Mechanical seal | lnertol Poxitar for standard applications |
Corrosion protection | Ceramic coating or the like for aggressive media, or according to customer request |
SAFETY
- The TSRM motor series is available in the "pressure-tight encapsulation" ignition protection type (Ex db) according to ATEX and IECEx for use in potentially explosive atmospheres (zones 1 and 2).
- PTC thermistor as overheating protection
- Temperature monitoring in the motor winding
- Monitoring of the sealing system by "streisal Toplimiter" leakage probe in the output end bearing plate
PRESSURISED WATER-TIGHT DRIVES
The submersible motors with IP 68 index of protection are frequently used as drives for pumps, agitators, scrapers and other units – for example, for pumping clear, dirty and waste water or slurries in municipal, industrial and private areas. Special applications such as lock drives, etc. are possible.
EXTREME OPERATING CONDITIONS
The motor series is available in the "pressure-tight encapsulation" ignition protection type (Ex db) according to ATEX and IECEx for use in potentially explosive atmospheres (zones 1 and 2).
The maximum medium temperature is 60 °C.
APPLICATIONS
-
Gas-tight cover feed-through for submersible agitator -
Submersible agitator in open storage tank -
Submersible agitator with installation fitting
ENERGY EFFICIENCY
The new series of highly efficient submersible motors is available with efficiency classes IE2 (high efficiency) and IE3 (premium efficiency). This reduces electricity consumption and saves energy costs.
ELECTRICAL CONFIGURATION AND CONTROL
The motor connection and the control connections are made by a shared, water-tight connecting cable which is configured to resist aggressive media.
Depending on the power rating and application, the motors can be operated with a direct connection, star-delta starting, soft starting or also with frequency inverters.
MOTOR SUSPENSION
Robust, sturdy attachment options are provided on the rear of the housing and on the side at the cable outlet, meaning that the add-ons (such as pumps, gearboxes, etc.) generally do not need to be used for suspension. The attachment axis on the solid cable outlet provides the opportunity of a swivelling option directly for the housing.
RELIABILITY
The shaft seal to the inside of the motor is always provided by a silicon carbide mechanical seal, and is therefore pressurised water-tight (IP 68). The standard equipment of our new series with ratings from 1.5 to 18.5 kW also includes temperature monitoring in the motor winding and a leakage probe for monitoring the leak tightness in the output end bearing plate.